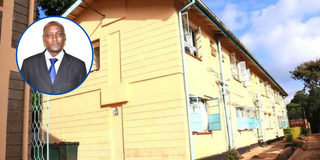
An image of Mt Kenya Hostel at the University of Embu after repairs using Cracksfox, a self-healing concrete. Inset: Professor Jackson Wachira Muthengia, an associate professor of cement, chemistry and concrete technology at the university.
Tiny cracks in concrete are the prelude to structural weaknesses in many buildings. A pore here, another there and before you know it, a crack is forming. Not to mention the water damage that follows these tiny cracks. These challenges drive up the cost of maintaining concrete buildings in Kenya, adding to the already burdensome cost of construction. But Kenya’s construction industry is experiencing a quiet revolution. There’s a shift from enduring high construction costs and unending maintenance budgets to innovation.
Part of this revolution is at the University of Embu where we meet Professor Jackson Muthengia, the Registrar, Academics Research and Extension, an Associate Professor of Cement, Chemistry and Concrete Technology at the University, as well as the CEO and Founder of Cracksfox Limited.
It has been about 25 years since Prof Muthengia began researching cement and concrete, and one of his groundbreaking research projects is on its way from lab to market. DN2 Property had an insightful interview with the industrious professor, who shares more about the science behind cracks in concrete and his innovation, Cracksfox, a first-of-its-kind self-healing concrete.
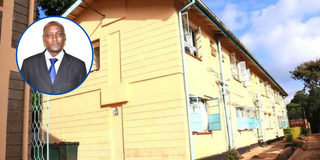
An image of Mt Kenya Hostel at the University of Embu after repairs using Cracksfox, a self-healing concrete. Inset: Professor Jackson Wachira Muthengia, an associate professor of cement, chemistry and concrete technology at the university.
The journey
Prof. Muthengia began researching on the field of concrete and cement technology in 2000 when studying his masters degree in Chemistry at Kenyatta University before proceeding to study a PhD in the same area.
“When I started working in cement and concrete research, the biggest issue at the time was the high cost of building with concrete. Between 2000 and 2003, we developed a highly substituted alternative cement. In layman’s terms, we took the regular cement, and added other supplementary cementitious materials (SCMs) as a partial replacement for Ordinary Portland Cement (OPC). Supplementing OPC lowers the cost of cement significantly. At that time, the standards limited us from adding beyond 25 per cent of the SCM to OPC. But the question was whether the limitations were necessary - because we do not need excessively high-strength cement. We worked with several stakeholders and discovered we could supplement as high as 60 per cent. This unlocked more research work and subsequent advancements in cement standardisation”.

Professor Jackson Wachira Muthengia is an associate professor of cement, chemistry and concrete technology at the University of Embu, as well as being the CEO and founder of Cracksfox Limited.
After this research project, another challenge presented itself, which prompted the groundbreaking research. In developing countries, cement is one of the most commonly used construction materials. The biggest challenge in most construction sites is the water used in mixing the concrete (cement plus aggregates), largely because water scarcity is quite common.
“One of my students in the cement industry reported a challenge where cement performs differently in different regions, even when the quality of the cement is the same across the board. We realised that besides differences in workmanship, water is the biggest problem. Different regions use different water sources and this makes all the difference in the quality of the concrete. But we cannot task standardisation agencies to regulate or develop standards for the water used in construction sites as this is nearly impossible. We had to figure out how to solve the challenge”.
How salt damages buildings
Many construction projects rely on salty water from boreholes, wells, and salty lakes. In some cases people use stagnant rain water which may be contaminated, and in rare cases some use sewage water which is extremely salty. And even when buildings are completed successfully, during their lifecycle they are still exposed to salty water.
Salt is extremely detrimental to concrete and often causes cracks, which may be visible to the naked eye but sometimes look like tiny pores especially on fresh concrete. If these cracks are not sealed early enough, they create an avenue for more salt to penetrate the concrete, leading to larger cracks and structural damage.
On where these salts come from, Prof Muthengia explains, there are two most common salts - sulphates and chlorides, and they are everywhere. There are four or five types of sulphates - first we have hydrogen reducing bacteria found naturally in any environment with limited oxygen. Sulphates are also common in approved preservatives used in almost all preserved foods. They are in fertilizers, soaps and detergents, and baking ingredients. As long as people are using these products, these salts end up in the soil or water sources. Sulphates are also found in most oceans. It is the most commonly available salt. Chloride is found in the normal sodium table salt we use. We also have such salts in borehole water. Sea water also has very high concentrations of salts.
These two salts damage concrete in different styles. Sulphates for instance, cause water to evaporate when they penetrate concrete. This allows more sulphates to penetrate the concrete. That process of dehydration and hydration creates expansive sulphate salt- meaning the salt expands. “It is a very small expansion but in chemistry it is crucial because it can cause cracks in very compact structures. The process is very slow and hard to notice - which makes it even more dangerous because your eyes adjust to the difference slowly and easily. It lacks the shock value, and by the time you notice, the cracks are too big”. Chloride corrodes and eats into the reinforcing or rebar metals used alongside concrete in construction. Ultimately, the corrosion causes cracks and structural failure.
Even when the cracks are invisible, cracked concrete may manifest in a similar manner as waterproofing issues. Common signs will include peeling paint and the absorbed salts will leave whitish deposits on the walls, especially in wet areas. Sometimes the walls develop green coloured matter. The walls and floors may also start leaking. In a few cases, buildings may develop visible cracks or collapse entirely.
Currently, there are several commercial solutions but they are not self-healing, as a result, property owners are subjected to endless maintenance and repair work.
Self-healing abilities and more
“To come up with a product that repairs the concrete again and again, throughout its life cycle, we conducted a lot of research, including pushing cement companies to grind cement to finer levels. We also tried working with available admixtures but nothing was working. We then resorted to simulating the two most common salts to try and find a solution. For example, if we wanted to test the impact of sewer water on concrete, we first establish the salt concentration levels and then simulate those conditions to higher concentration levels. After a lot of research work, we were able to find active ingredients which we used to design a first-of-its-kind admixture that responds every time there is a crack in a building where the admixture has been used. We called the innovation Cracksfox, and patented it”.
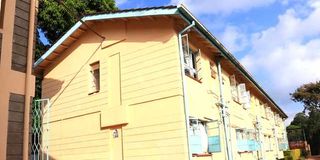
Essentially, when used during construction, Cracksfox seals any cracks that may appear during the early stages, and as the concrete hardens, any new cracks are sealed immediately as they appear, and this prevents future cracks. It prevents such cracks from forming for over 50 years in the lifespan of the building, a factor that prolongs the building’s life cycle. The active ingredient has been confirmed in lab tests to have a lifespan of over 200 years. This ingredient chemically binds those aggressive salts making them unavailable to damage the concrete.
Beyond the self-healing abilities, Prof Muthengia explains Cracksfox is also supposed to reduce the amount of water used when mixing concrete or mortar. And this is very important for water-scarce regions. In many building projects, fundis rely on water, which they may keep adding when mixing their concrete, but water tends to evaporate as the concrete cures immediately after construction. Once the water evaporates, the concrete may develop pores. Reducing the amount of water used during construction is therefore a great way to improve the concrete’s quality. They are also looking into extending the product’s application to road surfacing.
The product also acts as a waterproofing agent for substructures, septic tanks and flat roofs, and also improves the early strength of concrete. Normally, fundis are advised to build just four layers of walling per day, but with a product like Cracksfox, the concrete’s strength is amplified, making it possible to build more layers depending on the weight of the walling materials used. Ultimately, this improves the construction speed and may cut down on labour cost in the long run.
Durability tests
Although Cracksfox has not gone commercial, the product has undergone many tests to establish its viability and performance.
“We have conducted many tests in our lab and in a number of cement manufacturing labs. One of the tests is the chloride and sulphate penetration tests. In technical terms, this is called the diffusivity tests. We’ve also done absorptivity tests and we have subjected the product to aggressive conditions of high concentrations of acid, sulphate salts, chloride salts, simulated sewerage waters and sea water. Subjecting the product to these diverse environments helped us observe the level of cracking, the strength it loses, pore formation and how well it performs in crack repair”.
“We’ve done flexural strength and compressive strength testing. We also tested the setting time of the concrete and researched on the compounds formed when used alongside cement. We have also compared the performance of Ordinary Portland Cement when used in combination with our product versus cement without Cracksfox versus cement mixed with other commercial admixtures. The results are impressive. Lastly, we conducted permeability tests and micrograph tests which helped us identify how well the cracks are sealed. These tests magnify the microstructure of the concrete, making it possible to observe defects that would not otherwise be visible to the human eye. With such tests, we can tell whether the concrete has sealed, how it has sealed and the types of compounds it forms.
Applications in real construction projects and projected cost
To further test the admixture’s performance in real world construction projects, Prof Muthengia says it has been used in several building projects. In October 2024, Cracksfox was used to repair one of the hostels at the Embu University.
“Every year when the students go on long holiday, the administration has to repair the washrooms. When we developed Cracksfox, I was asked if we can offer the product free of charge for repair work. It was used and the results are amazing to date”.
It has also been used in the substructure and walling of a separate construction project at the university. In Thika, the product was further put to the test in a two-storey building. It has also been used in a project with a hidden roof, and for water tank repair projects.
Once it hits the market, Cracksfox can be used either during construction or for repairing cracks. When used during construction, one bag of cement is supposed to be mixed with two kilograms of Cracksfox.
“Though we are yet to mass produce or commercialise the product, the projected market price is Sh300 per 2 kilograms for retail and Sh240 if buying wholesale. These prices will most probably reduce with mass production.”
Challenges in moving from lab to market
Like many other brilliant research projects, moving from lab to market comes with a unique set of challenges.
Prof Muthengia says, “We’ve had a lot of development in self-healing technology and the biggest challenge has been moving groundbreaking research from lab to market. True invention is in scaling such products to the market. Our research spanned over 20 years. The first product we created had a very short shelf life of about a week, so it was not viable. This was our biggest hurdle in the beginning but we ended up creating an improved product with a shelf life of more than seven years.”
Beyond turning an incredible idea into a tangible product, the other obstacles are the capital required to invest in large scale production equipment, while establishing adequate human resource capacity is also challenging.
“For now, there is a team that supports me in the lab, but to scale we would need a larger team that can run a manufacturing company.”
Reaching the market is also not easy. That would entail creating distribution systems in a way that people can access the product from different regions. The professor notes, “We have brilliant minds in Kenya, and if we can create a system where academia is seamlessly connected to industries, universities will be self-sustaining.”
The professor also urges stakeholders in construction, including the government, to partner for innovations like Cracksfox to cross over to the market.
“We are open to partnerships with the stakeholders in research, production, regulatory bodies and construction professionals.”
So far, the team has partnered with several agencies and institutions in trying to scale the product.
“We are working with several partners who are helping us move the product from the lab to the market. One of these partners is the Kenya National Innovation Agency (KeNIA). They’ve been instrumental in training us on how to develop the product, managing finances, looking for investors, how to run a company and everything required for a successful transition. Cracksfox won the Presidential Innovation Challenge and Awards (PIA), 2024/25 - as the second runners up. They are also engaged with the University of Michigan to explore further research on how to diversify Cracksfox into several products, and are moving into scaling what they have now, supported by KeNIA through the Research to Commercialisation Program (R2C).
“They’ve also connected us with a number of sponsors. We have considered a licensing model which entails permitting use of the technology and production of Cracksfox in exchange for royalties, and have also engaged international companies in trying to explore different ways of scaling”.