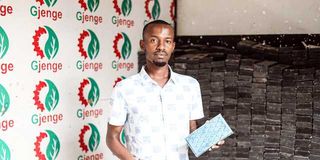
Gjenge Makers Sales Executive John Luka showing bricks made from recycled plastic at the company’s factory along Butere Road in Nairobi on May 28, 2025.
The first thing John Luka, the marketing executive at Gjenge Makers Limited does when you visit the factory on Butere Road, Nairobi, is pick up a brick, and as forcefully as he can, drop it on the floor to showcase its superior quality.
Gjenge is a pioneering company that transforms plastic waste into high-quality PV bricks, an alternative for concrete blocks commonly used in paving roads and walkways in commercial and residential spaces.
The company is headed by a female entrepreneur—Nzambi Matee, a Kenyan trained mechanical engineer, environmentalist, and hardware designer.
Gjenge champions environmental sustainability by recycling plastic waste that would otherwise contribute to pollution. They started operations in 2019.
“We started with three employees, and two machines—a hydraulic press and an extruder, then, we used to outsource the services of a crushing machine,” says Gjenge Makers Sales Executive John Luka.
By crushing and blending the plastic waste with sand, the business produces durable bricks that outperform traditional concrete blocks.
This innovation not only mitigates environmental damage, but also offers a cost effective and long-lasting solution for pavement construction.
“The bricks are made in different colours. We have black, which is the colour of plastic subjected to heat and by far our biggest production in terms of volume, we also have other colours like blue, green, red and grey.
We master colour batch or virgin plastic to suit the needs of the clients,” Luka explains, adding that they procure this waste from aggregators and industries in the larger Nairobi metropolis.
“We have two main raw materials—plastics and sand. We use locally available river sand. For the plastics, we source from post-industrial and post-consumer aggregation.”
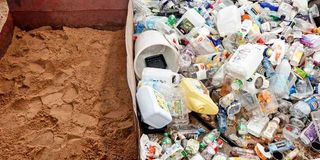
Plastics to be recycled pictured at Gjenge Makers Limited located along Butere Road in Nairobi on May 28, 2025.
Post-industrial is any plastic they get from industries. It could be that they are out of desired shape or they are no-longer useful in their manufacturing process.
For the post-consumer is the waste that comes directly from residential and commercial spaces. For this category, they collect from the dump sites.
They are also in a pilot phase of a collaborative collection channel with an estate in Kiambu, where they have a designated area where residents pile all their plastic waste, which the company collects for use at the plant.
They use three different types of plastics.
“We collect Low-Density Polyethelyne, High-Density Polyethelyne and Propylene. Our sorting process is rigorous to ensure that we only use those three for quality purposes.
Since we receive all manner of plastics especially through the post-consumer sources, we usually have those we don’t need.
It is our principle to reduce the plastic pollution to the environment as much as we can, so we dispose those categories of plastic that we don’t use to aggregators who recycle them.”
To further reduce harm to the environment, they insist on sun-drying their sand instead of continuously using electricity.
“It might not be a big thing to do that, but our commitment to sustainability does not look at any efforts as insignificant. We believe that all steps taken toward making the environment safer are giant and important,” explains Luka.
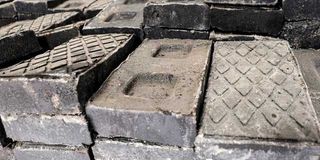
Samples of bricks made from recycled plastic at Gjenge Makers Limited located along Butere Road in Nairobi pictured on May 28, 2025.
Gjenge designs and fabricates and tests all their machines locally.
“Our machines are locally designed. We are lucky to be a pioneering entity with enviable industry knowledge understand.
This skillset has improved our efficiency and cost-cutting imperatives significantly and has also opened up a market we didn’t know existed—that of selling machinery to other parts of the continent. We recently shipped one to a West African country.”
So, how exactly does plastic transform into an extra strong paving brick?
“The process begins by crushing it into small shards of about 8mm. This makes for a perfect size to build the blend. After mixing, the blend is taken to the extruder where we expose it to heat at between 340 -370 degrees.
The plastic acts as the adhesive agent, just as cement works in concrete. This comes out as molten material that is taken to the weighing scale.
It is important that we have the right weight because this is a determinant to how strong the bricks will become and the amount of weight they will withstand. The molten material will then go to the hydraulic press where real bricks are made. It is at this stage where cooling is done.”
Gjenge makes three gauges of pavers, high, medium and heavy-duty bricks. The high-duty ones weigh about 1.3Kg and can stand a force of about 100N/mm².
The medium-duty ones weight about 1.5Kgs and can stand a force of about 164N/mm², while the last category—the heavy-duty pavers, can stand a force of about 200N/mm² and weigh 1.7Kg.
Perhaps their biggest win is their turnaround time. “Concrete pavers have a standard six to seven days for the curing process, while our bricks take about 10 minutes to cool down and are ready for use immediately.
Additionally, unlike concrete bricks, we do not have breakages because our bricks have a compression strength that is three times more than that of conventional concrete pavers.
So, if you want to pave a patch in your residence or a commercial space, we advise buying exactly what you need.”
They make about 1,500 pavers on their two-shift a day working arrangement. They have employed 20 people directly and about 120 indirectly, improving living standards to tens of family in the city.
The demand for Gjenge’s pavers has steadily increased, a fact Luka credits to the pavers’ superior quality and resilience.
The business wants to expand their level of impact by having material recycling facilities across the Nairobi metropolis, where the plastic waste they receive will be crushed on site and transported easily to their Butere Road facility.
They plan on increasing their production to about 4,000 pavers per day.