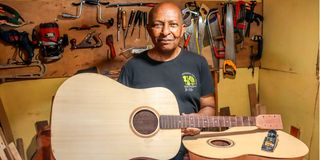
Luthier Solutions owner Kenneth Mlamba at his workshop in Kikuyu, Kiambu County on April 18, 2025.
If you ever wondered who is responsible for the smooth sounds of a well-tuned guitar or the rich tone of a beautifully restored violin, look no further than the luthiers.
In Kikuyu, Kiambu County, Kenneth Mlamba is immersed in the art of guitar making, his workshop alive with the sounds of craftsmanship. Cutting, shaping and winding with precision, he transforms raw wood into finely tuned instruments.
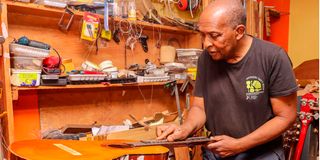
Luthier Solutions owner Kenneth Mlamba repairs a guitar at his workshop in Kikuyu, Kiambu County on April 18, 2025.
His hands move with expert agility as he meticulously carves the body, adjusts the neck and strings the guitar to perfection.
This dedicated luthier has spent decades transforming raw materials into instruments that bring music to life. Mr Mlamba has turned his love of craftsmanship into a remarkable journey of guitar making.
His first creation, an electric guitar shaped with a machete, was the start of a passion that would develop into a career spanning over 50 years.
“My background is in human resources, but I have always been drawn to working with wood and even stone. In 1971, I built my first guitar, and that moment changed everything. After retiring, I turned what had been a personal passion into a full-time pursuit,” he says, adding that by the time luthiery became his career, he had already invested in a good set of tools and had even made some himself.
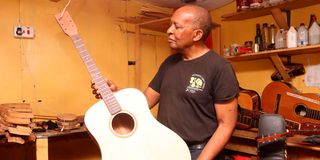
Luthier Solutions owner Kenneth Mlamba at his workshop in Kikuyu, Kiambu County on April 18, 2025.
With a starting capital of Sh70,000 from his savings, he set up his company and began producing a variety of guitars. His creations include solid body electric guitars, electric and semi-acoustic basses, steel string acoustic and semi-acoustic guitars, and classical acoustic and semi-acoustic guitars.
“Over the years, I have built and customised guitars for renowned musicians, including Kato Change, Polycarp of Sauti Sol, and Nyatiti for Makadem and Susan Owiyo,” he says.
Mr Mlamba makes custom guitars and offers repair services for a wide range of stringed instruments. His expertise extends to traditional African instruments such as the kambanane, nyatiti, banjos, mandolins, sitars and the violin family of instruments.
"Each instrument is a unique challenge, requiring attention to detail and a deep understanding of its cultural and structural nuances," he notes.
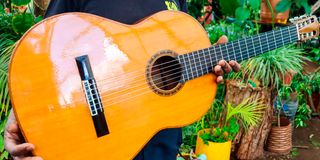
Luthier Solutions owner Kenneth Mlamba holds a guitar at his workshop in Kikuyu, Kiambu County on April 18, 2025.
Precision is the order of the day as he meticulously shapes, assembles and repairs instruments in his workshop.
Making a guitar from scratch is a complex process that requires meticulous attention to detail. He begins by determining the type of guitar he will build, whether it be a steel string acoustic, electric, semi-acoustic or solid body bass.
“I consult with clients to understand their preferences and carefully select materials accordingly. Most of the materials I use are locally sourced. The backs and sides of my acoustic guitars are typically made from Kenyan mahogany, which is abundant in the region,” he says, adding that Kenyan mahogany has a rich, warm tone that complements the sound.
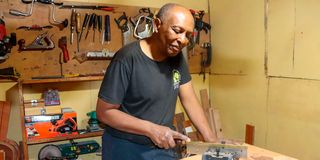
Luthier Solutions owner Kenneth Mlamba cuts fret slots of a guitar at his workshop in Kikuyu, Kiambu County on April 18, 2025.
For high-end guitars, however, he imports spruce for the soundboard, recognising its superior tonal quality and global reputation. The additional cost of these imported materials is passed on to the customer.
The guitar-making process begins with the preparation of the wood, which is cut to shape and fitted into the required form. The sides of the guitar are bent and glued in place, linings are added for reinforcement and the neck is carefully fitted.
Once the structure is assembled, he carves and attaches the fretboard and bridge, then applies the final finish before adding the strings. “Each guitar takes about six to eight weeks to complete, though I often work on multiple projects at once to maximise efficiency," he shares.
Prices start at Sh40,000 for a basic acoustic guitar, with high-end electric models going for up to Sh200,000.
“I welcome competition to challenge myself to create better instruments. My guitars are not mass-produced like those made in factories; they are custom-made for specific customers. This allows me to give each one individualised attention to meet their unique needs,” he says.
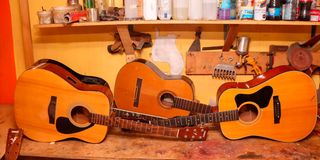
Guitars for repair pictured at Kenneth Mlamba’s workshop in Kikuyu, Kiambu County on April 18, 2025.
Mr Mlamba's craftsmanship has earned him recognition beyond borders, with orders from international clients including musicians from Finland, Germany, USA, UK and Sweden.
His distinctive approach, which incorporates African materials and designs, sets his instruments apart in the global marketplace. "What sets my instruments apart is not just the quality of craftsmanship but the unique integration of African materials that give each piece its own character," he explains.
While the general shape and design of his guitars remain consistent, his craftsmanship is distinguished by his expertise and choice of unique materials. He often uses African Blackwood – a rare and highly prized tonewood often referred to as the "holy grail" of guitar making – for the back and sides.
“Its dense, hard nature produces a tight, powerful sound with crisp, bell-like overtones, excellent clarity, and strong note separation and sustain. For necks, sides and backs, I commonly use locally sourced mahogany. It is strong, workable, attractive, readily available, and produces a warm, sustained tone,” he explains.
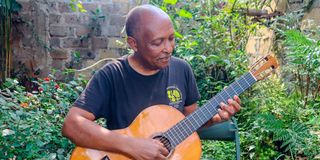
Luthier Solutions owner Kenneth Mlamba plays a guitar at his workshop in Kikuyu, Kiambu County on April 18, 2025.
When it comes to the soundboard, he prefers imported spruce for its superior tonal characteristics. “Woods from temperate climates like spruce have more pronounced annular rings than those from tropical regions due to the distinct seasons. These rings are crucial for sound production,” he adds.
He also customises the aesthetic elements of his guitars by adding African-themed rosettes around the soundhole, turning each piece into a work of art. "It is about merging form and function, creating something as beautiful to look at as it is to play.”
His favourite instrument to make is the classical nylon-string guitar, which he carefully designs using a combination of imported spruce and local mahogany.
Mr Mlamba says he is constantly looking for ways to improve his efficiency by exploring new tools and learning innovative methods through information technology for cutting, measuring and finishing.
His workshop is a one-man operation. He compares it to painting a picture, where you do not necessarily have other artists working for you. However, he does occasionally mentor an apprentice to pass on the skills.
“The art of guitar making, particularly the modern classical guitar shape, originated in Spain, but it has since spread worldwide. Although Africa may still be a bit behind, the digital age does not signify the end of luthiery; it simply provides a new perspective on creation," he says.
He adds that there is still a niche market for customers who prefer handmade instruments that are tailored specifically to them. "There is something special about purchasing a picture painted by hand rather than a machine-printed copy.”